Très compacts, puissants et polyvalents, les amplis Powersoft requièrent différentes étapes dans le processus de fabrication, depuis la pose des CMS (composants montés en surface) jusqu’à l’assemblage final.
Nous sommes allés à Scandicci (le siège, à côté de Florence) et à San Giovanni in Persiceto, à côté de Bologne (chez le sous-traitant des cartes électroniques), les voir naître sur des lignes très automatisées, guidés et informés tout au long de notre visite par Antonio Peruch, un des trois fondateurs de Powersoft, qui chapeaute toute la partie industrialisation : fabrication, test et process, du fabricant transalpin.
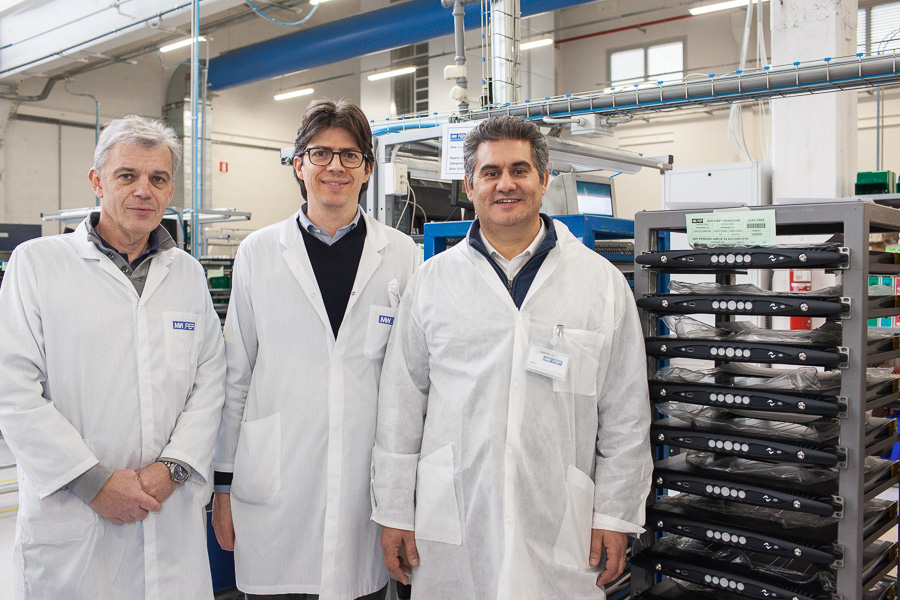
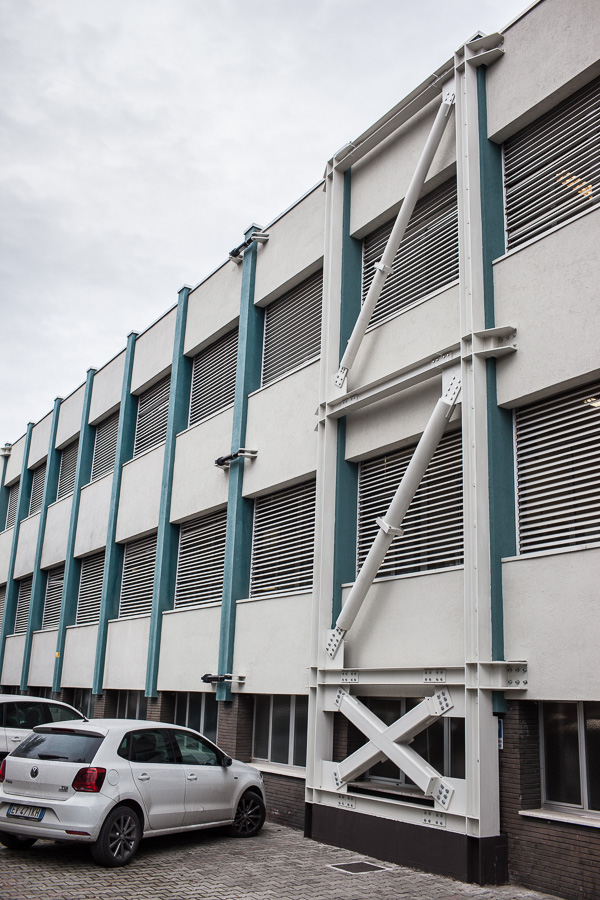
Débutons notre périple par l’usine MW.FEP de San Giovanni où Antonio nous emmène en premier et où sont assemblées et testées toutes les cartes des plateformes d’amplification Powersoft entant dans les amplificateurs en rack (toutes les séries). Cette usine du groupe Meta System est un des fleurons de l’industrie italienne EMS (Electronic Manufacturing Services).
Pour la petite histoire, les bâtiments ont fait l’objet d’aménagements anti-sismiques « up to date » car la terre tremble de ce côté des Apennins. De même l’usine est « green », comme les amplis Powersoft, et couvre une partie de ses besoins énergétiques par panneaux solaires, environ la moitié de la consommation totale annuelle, et pratique le recyclage. Cette usine produit environ 100 000 cartes Powersoft par an (tous modèles confondus).
Sur les 9000 m2 de l’implantation, 6000 m² sont réservés aux différentes lignes de production, et la « partie » Powersoft en occupe à peu près la moitié. Cela comprend aussi bien des lignes complètes CMS (pour composants montés en surface) par refusion que des lignes de soudure à la vague et même des vagues sélectives* pour les composants traversants, le tout à la pointe des technologies en vigueur actuellement, plus évidemment des lignes de contrôle.
* Dans une vague sélective, la carte ne passe pas sur un lit de soudure en fusion mais une buse vient déposer (par dessous) la soudure sur chaque point à souder selon un repérage topographique. Ce n’est bien sûr valable que si le nombre de traversants implantés reste faible mais il n’y aucun risque pour les CMS déjà posés.
Pour les cartes CMS, les machines à implanter installées acceptent des tailles jusqu’à des empreintes 0201 (0,2 x 0,1 dixièmes de pouce, soit environ 0,5 x 0,25 mm) et les composants en boitiers BGA (Ball Grid Array ou matrice de billes) avec les outils d’inspection associés. Certaines cartes Powersoft sont implantées des deux cotés sur des circuits imprimés (époxy, FR4) comprenant jusqu’à huit couches. C’est le cas notamment de la carte numérique de la série X qui accueille un DSP Texas Instruments en boitier BGA de 1031 pins. Cette carte comporte 1867 composants et 5337 points de brasage en double reflow (implantation sur les deux faces).
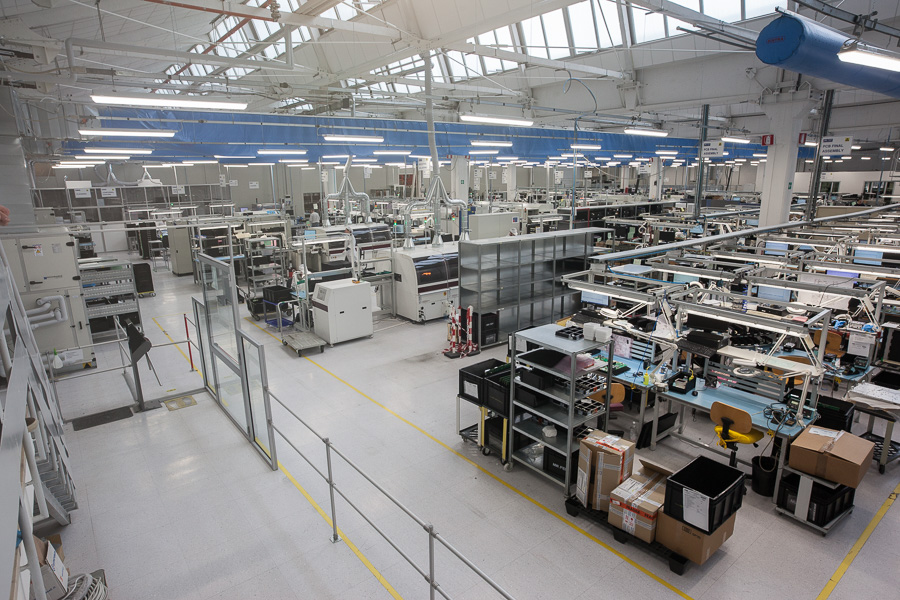
Les étapes d’assemblage des cartes (qu’on peut voir sur les différentes photos d’accompagnement) débutent par le dépôt de pâte à braser sur les zones d’accueil des composants (pads) à l’aide d’un pochoir (stencil) spécifique à chaque carte. Ensuite la carte passe dans une machine à implanter automatique qui dépose les composants au bon endroit (et dans le bon sens) avec leurs coordonnées XY, et en général les CMS sont chargés sur des bobines qui contiennent de 2000 à 4000 pièces pour ce qui concerne ce qu’on appelle les « commodities », résistances, transistors, diodes, inductances et condensateurs CMS petit format. Pour certains composants, cela peut être des tubes (certains circuits intégrés, relais ou autres).
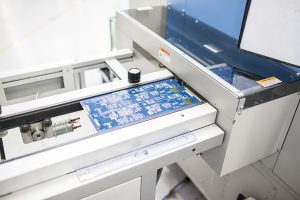
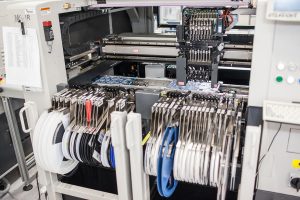
Ensuite la carte passe dans un tunnel de refusion (four) où la température monte par pallier (par zones) jusqu’à un pallier haut de 1 à 2 minutes et redescend progressivement. Le profil de montée en température, de temps d’étale (température max) et de descente est important (crucial) et dépend d’une part des composants (selon les specs des fabricants à respecter) mais également de la géométrie de la carte et du volume des éléments.

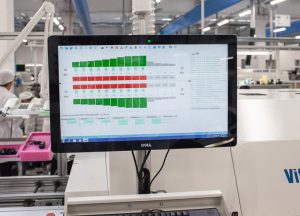
Par ailleurs la géométrie, la surface des empreintes des plages d’accueil de la pâte et leur espacement l’est également, mais cela est du ressort des spécialistes CAO des circuits imprimés (éventuellement en interaction avec le sous-traitant) et est parfaitement maîtrisé chez Powersoft.
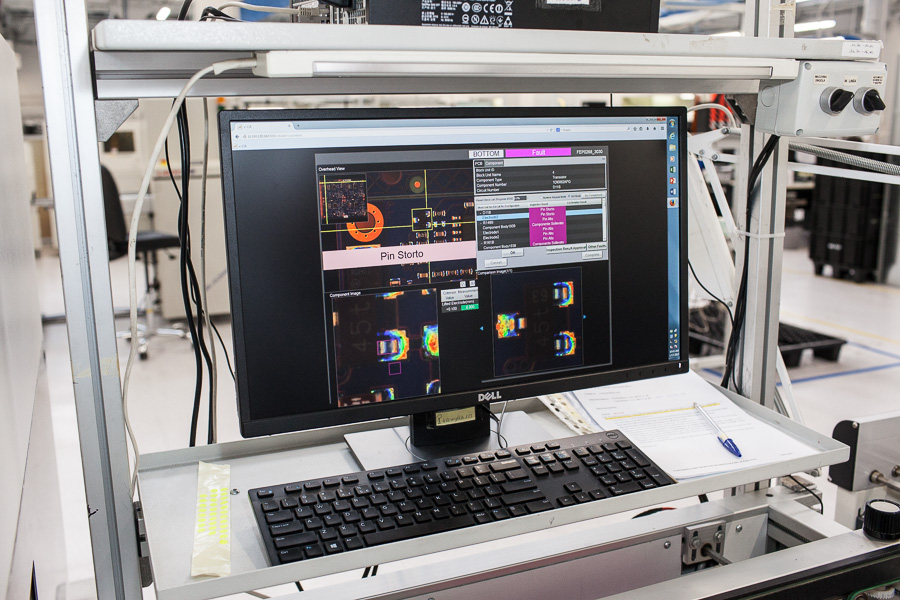
Puis une première inspection visuelle est opérée (pour 100 % des cartes chez Powersoft) dans une machine en automatique (AOI, Automatic Optical Inspection) en 2 ou 3D à l’aide de caméras et d’un logiciel à auto-apprentissage. Lors de notre visite nous avons pu voir l’apprentissage en 3D sur une carte où on contrôle l’aspect des joints de brasage, des dépôts, et le positionnement des composants (qui peuvent se soulever par exemple lors de la refusion).
A noter que depuis l’entrée des composants et leur lot et le numéro de carte, tout fait l’objet d’un suivi (tracking) informatique tout au long de la fabrication, de façon à pouvoir analyser les problèmes ultérieurement. Le temps de stockage des composants de type BGA (bien qu’ils le soient dans les conditions ad hoc) est aussi contrôlé, pour des raisons de rétention d’humidité notamment qui pourrait contrarier le processus de refusion. Dans le cas des cartes avec implantation CMS sur les deux faces, il faut répéter les opérations précédentes pour la deuxième couche. Pour le contrôle de l’implantation de BGA, l’inspection « visuelle » n’est pas possible et cela s’opère par rayons X.
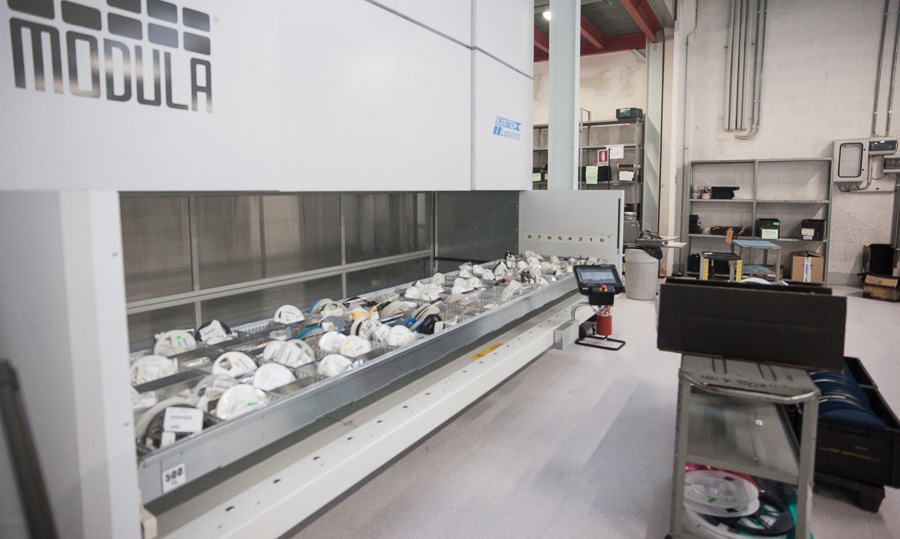
En ce qui concerne la pose des composants traversants (transfos, selfs, gros condensateurs chimiques, etc.), certains sont placés en manuel et le brasage s’effectue à la vague. Si la carte comprend une prépose CMS coté composants, pas de problème, sinon on procède par masquage (de la partie CMS) ou alors en vague sélective où une buse vient placer le joint de soudure (selon les coordonnées XY de chaque composant à souder) sur chaque patte de traversant sans que tout le dessous de carte baigne dans la vague de soudure, procédure évidemment un peu plus gourmande en temps.
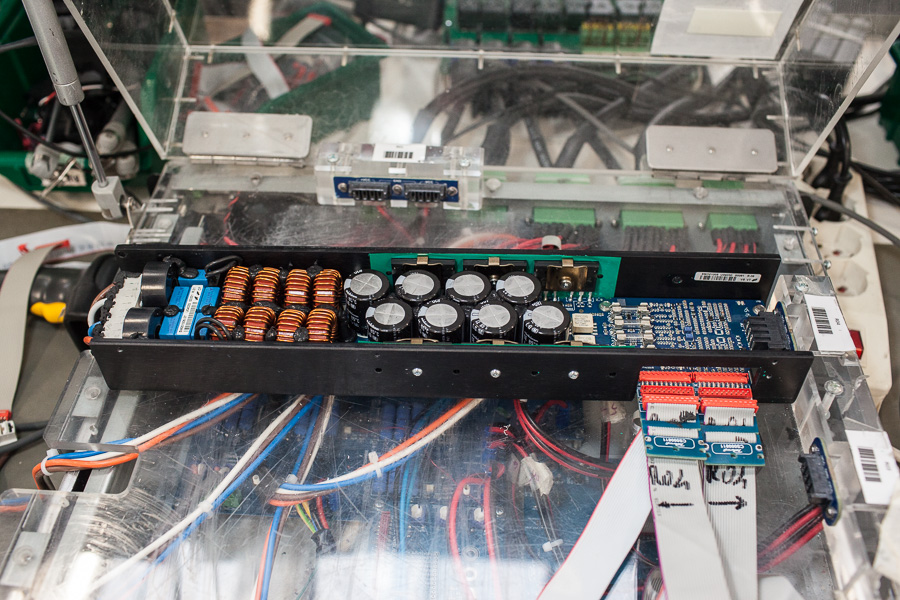
Lorsque le contrôle visuel est passé, par machine ou opérateur lorsqu’il n’y a que quelques traversants, on monte éventuellement les pièces manquantes tels que les dissipateurs sur les cartes de puissance, en manuel, et on procède ensuite à une phase de test sur des bancs (fabriqués sur mesure selon cahier des charges Powersoft), en ayant procédé au préalable à un contrôle visuel avec d’éventuelles retouches manuelles.
Ces bancs sont dotés d’un lit de clous (pointes de contact rétractables) placés en vis à vis des points de test choisis sur la carte, et sur lesquels la carte vient se placer en compression. On peut y adjoindre selon les cas des faisceaux sur les connecteurs.
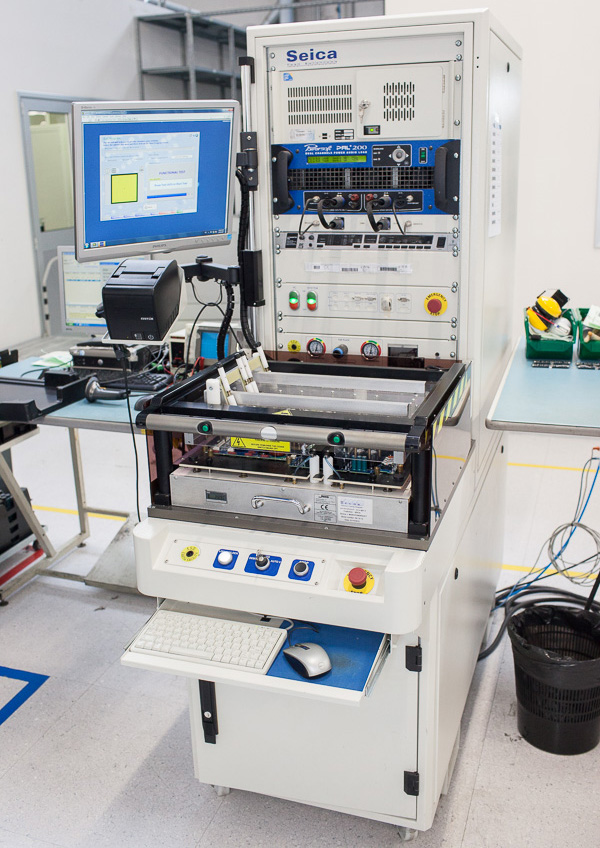
Cela permet d’envoyer des stimulis et de contrôler différentes réponses devant entrer dans des gabarits voire même de programmer in situ des composants programmables (micro-contrôleurs, DSP, EEPROM avec le « firmware »), ou encore de vérifier la tenue diélectrique (cartes d’alimentation), …, selon le type de carte et de banc.
De la sorte, on est certain que les différents sous-ensembles sont totalement opérationnels et répondent aux contraintes normalisées avant l’assemblage complet du produit. Là encore ces tests sont opérés sur la totalité des cartes et il y a donc autant de bancs que de types de sous-ensembles à tester selon les plateformes d’amplification (série K, série X, due, quattro et ottocanali, etc.).
Ensuite on procède à l’assemblage final des produits dans leur châssis puis à un test fonctionnel sur un banc informatisé avec un analyseur Audio Precision et des charges de puissance « maison ».
Ce test opéré par séquences (certaines en mode « fast test » où plusieurs mesures découlent des mêmes stimuli) dure environ sept minutes où on relève réponse en fréquence, rapport signal/bruit, distorsion, diaphonie, puissance, …,etc., et dont les résultats doivent entrer dans des gabarits (limites) pour que le produit soit conforme. Là encore tout est enregistré avec le numéro de série sur informatique.
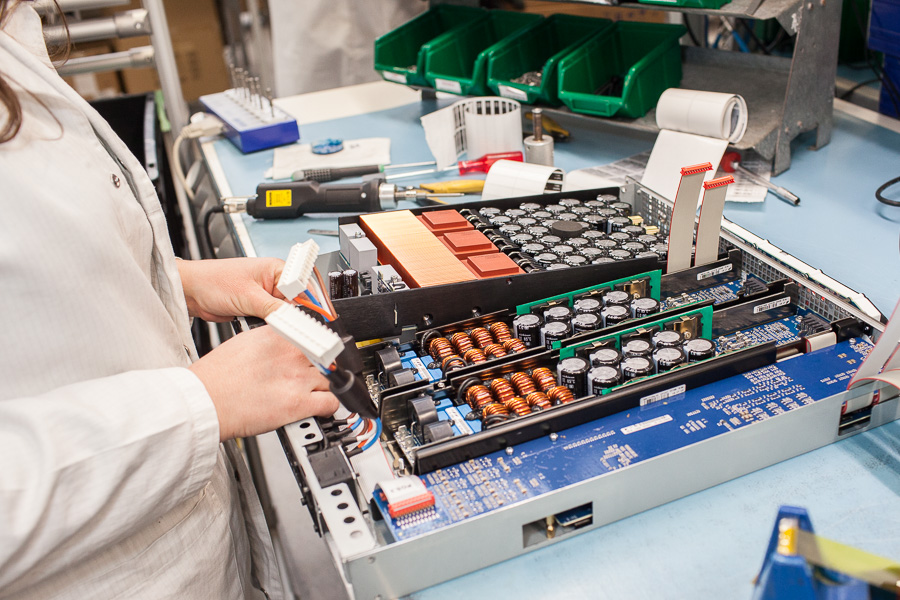
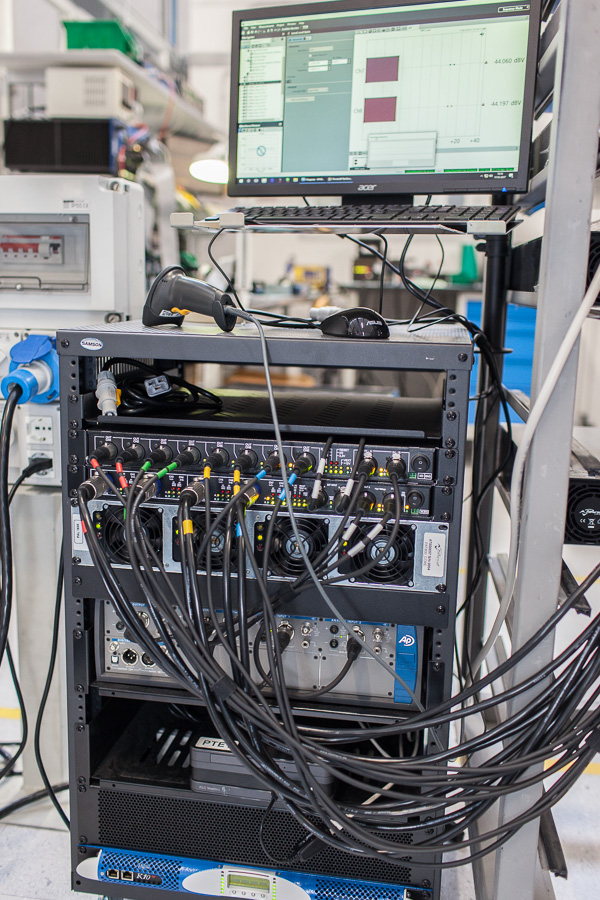
Jusqu’à l’année dernière, les appareils passaient ensuite dans une chambre sur des baies avec charges, liaisons réseau, où ils subissaient des tests d’endurance par cycle durant environ 4 heures avant de rejoindre la tour de stockage après emballage. Cela reste le cas pour une partie de la production mais Antonio a commencé à modifier le process durant 2017 et après avoir confié pendant 9 ans l’assemblage de ses amplis en rack à MW.FEP, Powersoft a fait le choix de rapatrier une grande partie de l’assemblage final au sein de son usine de Scandicci où, par le passé, elle procédait déjà à l’assemblage et à des phases de test qui duraient 3 jours !
Les modules amplificateurs (sauf les LiteMod) sont quant à eux toujours fabriqués dans une autre usine de MW.FEP dans le nord de l’Italie, à proximité de Trieste. Les raisons qui ont poussé Antonio Peruch et Powersoft à rapatrier l’assemblage sont le désir de rationaliser la fabrication, de limiter les stocks, de raccourcir les délais de livraison sous les 15 jours quelle que soit la référence commandée, de mieux accompagner la croissance de l’entreprise, mais aussi de simplifier la chaîne en facilitant la détection d’une panne, sa solution, et de raccourcir le test final fonctionnel puisque des vérifications constantes sont effectuées à chaque étape.
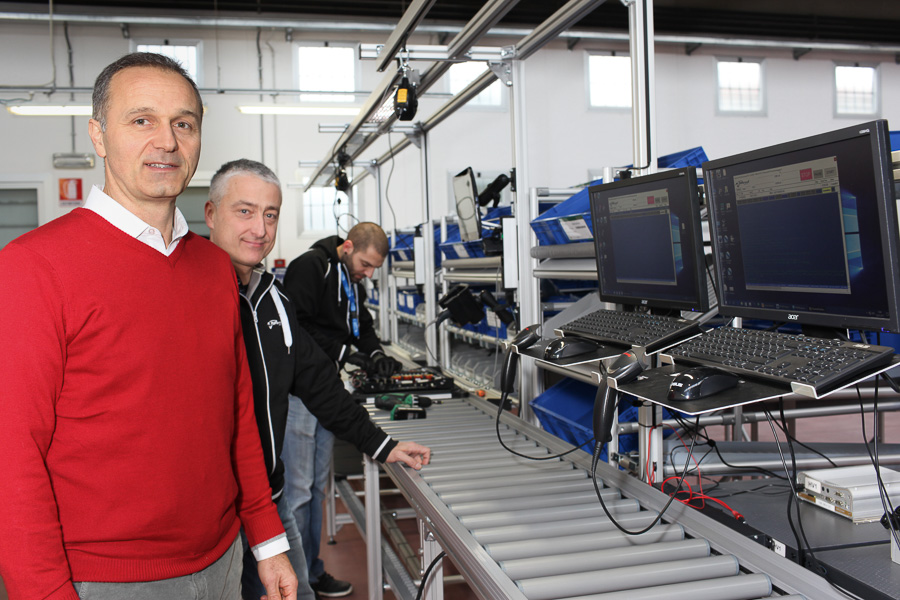
Puisqu’on parle de chaînes, elles sont désormais au nombre de 4 (à Scandicci) dans un bâtiment pouvant en contenir jusqu’à 6, et fonctionnent suivant le principe du Pull, un modèle japonais plus flexible et adaptable à de petites séries, à de l’OEM voire à du sur mesure que le classique Ford en vogue sur les chaînes de fabrication de voitures. Appelons aussi cela du One piece flow. Cela concerne pour l’heure les amplis de la série X et les nouveaux modèles pour l’installation, duecanali et quattrocanali.
L’assemblage dans son ensemble est placé sous la direction de Valter Cubattoli (homme au pull rouge) et Leonardo Magnolfi (pull noir et blanc) a en charge la direction opérative des chaînes. Pour revenir à ces dernières, elles sont alimentées par des bacs pré-chargés fournissant à l’opérateur précisément les pièces nécessaires à l’assemblage d’une série de produits. La chaîne est cadencée par le Takt Time, à savoir le temps calculé en divisant le nombre d’heures travaillées dans une semaine ou une journée par le nombre d’appareils en commande. Si le Takt Time chute en dessous du temps nécessaire à l’assemblage d’un produit, une ligne est ajoutée.
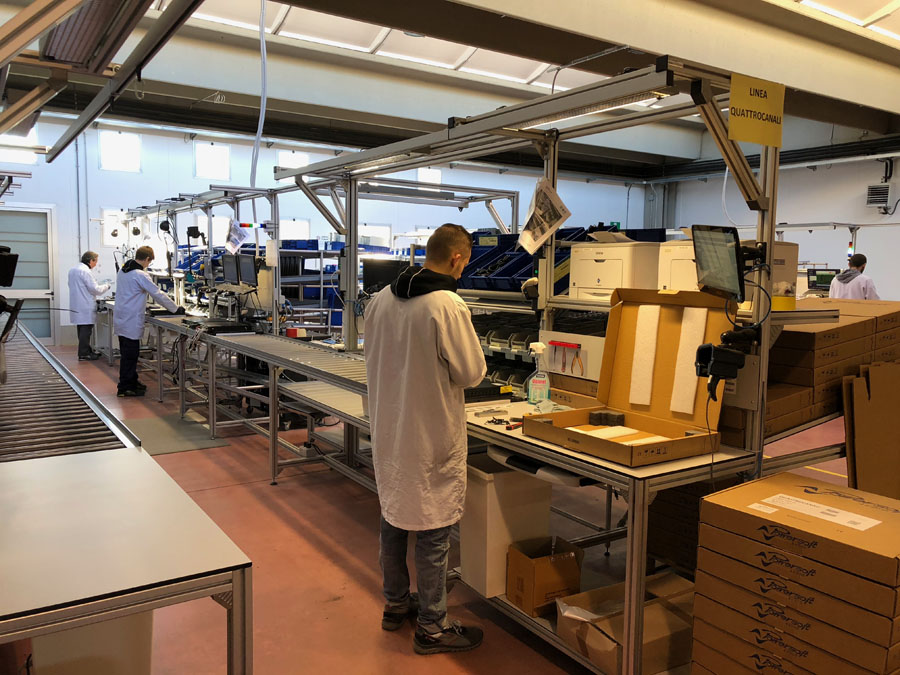
Chaque soir les bassines sont réapprovisionnées et replacées sur les convoyeurs et à terme ce seront les fournisseurs qui livreront directement les pièces dans les conteneurs adéquats. Le montage comporte en bout de chaîne, l’essai complet sur un banc informatisé validant l’ensemble des paramètres de l’ampli et lui donnant la possibilité après des cycles d’endurance d’être emballé et remis au logisticien.
Tout problème éventuel est immédiatement repéré et corrigé afin que les appareils suivants soient parfaits, sans oublier que tous les sous-ensembles (cartes de puissance, cartes d’alimentation et cartes de traitement, …) sont préalablement testés et contrôlés chez le sous-traitant qui assemble les cartes.
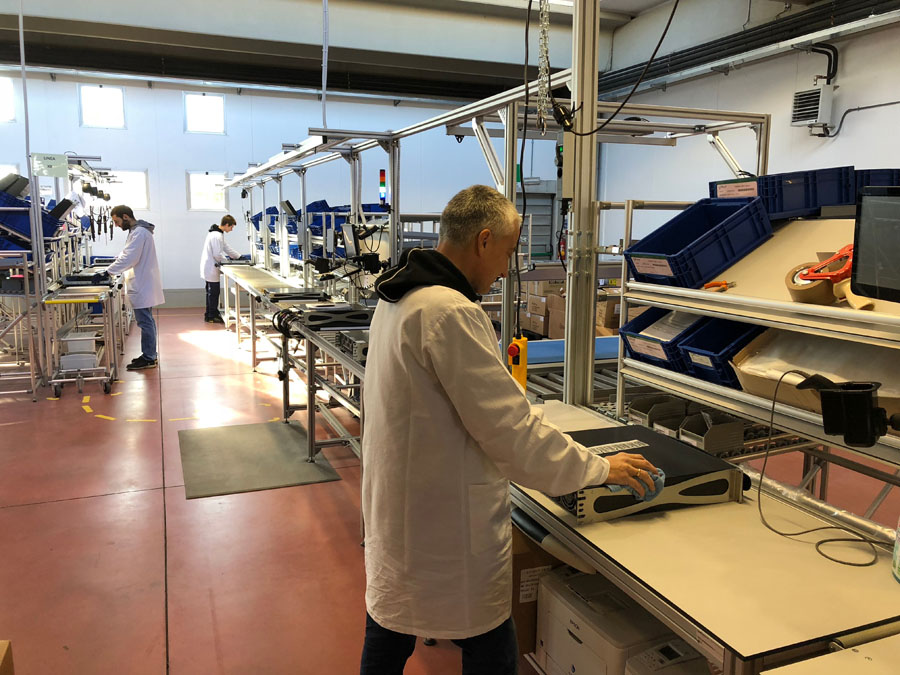
Deux lignes, ou plutôt une ligne en forme de Y est en charge de l’assemblage des X8 et X4, chaque référence disposant d’une branche du Y et l’ensemble des machines se rejoignant pour les phases de test. L’avantage de gérer son assemblage via des chaînes préfabriquées est de pouvoir les reconfigurer en très peu de temps en fonction du type de produit à assembler, de même qu’il est possible de doubler certains postes ou de déplacer par exemple celui de test.
La chaîne est donc vivante et se plie « en quelques coups de visseuse » aux besoins des clients de Powersoft. Comme nous le dit Antonio, c’est un vrai Lego.
SAV
Qui dit électronique dit aussi pannes (même si on fait tout pour les minimiser), d’où la présence à Scandicci d’un pôle SAV extrêmement bien pourvu en termes de pièces, schémas et techniciens qui comprennent le « Lastrucci » sur le bout des doigts ;0). Sur une population mondiale d’environ 410 000 pièces vendues depuis 2007, environ 1000 pièces (amplis et modules confondus) rentrent chaque année en SAV, y compris les tout premiers amplis de 1997 qui peuvent tout à fait être réparés.
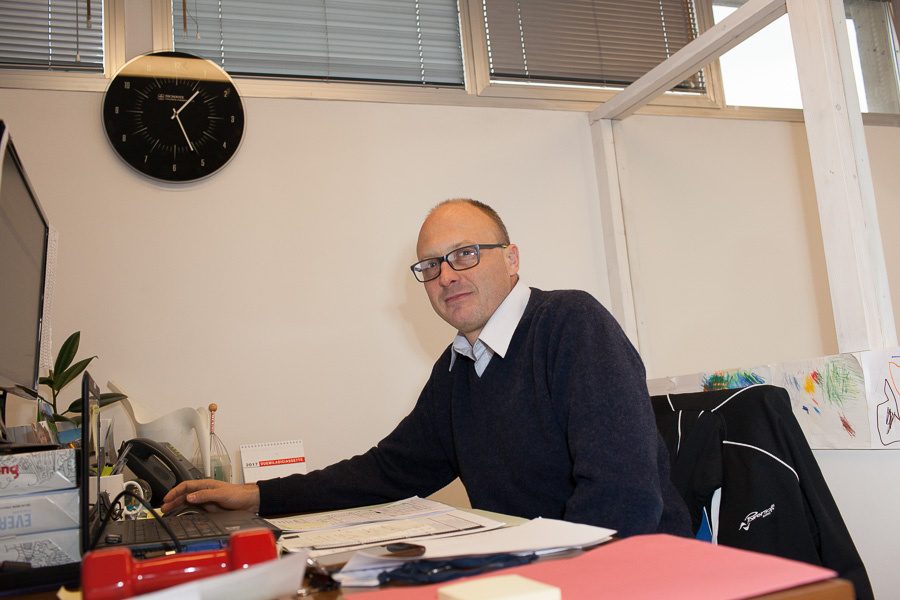
La technicité des produits Powersoft limite les possibilités pour les distributeurs et encore plus les utilisateurs de dépanner eux-mêmes les appareils ; Malgré tout, Marco Mannucci qui gère le Customer Care et le Factory Service Center de Scandicci, parcourt le monde pour former des techniciens de SAV des 34 Authorized Service Centers, 35 avec celui de Scandicci, couvrant les cinq continents afin de raccourcir les temps d’indisponibilité en cas de pannes bénignes.
Le pôle SAV de Scandicci comportant 4 personnes s’occupe de l’Italie mais aussi d’un certain nombre de pays européens qui, par leur proximité géographique avec ce pays, ne disposent pas de Service Centers, et réceptionne aussi bon nombre de modules OEM que les marques d’enceintes emploient mais n’ont pas la capacité de réparer. Les derniers modèles sont aussi systématiquement rapatriés. Rappelons ici que 1000 pièces par an représentent environ 4 appareils à dépanner par jour. Sur un parc vendu de 410 000, on peut dire que la marque est fiable.
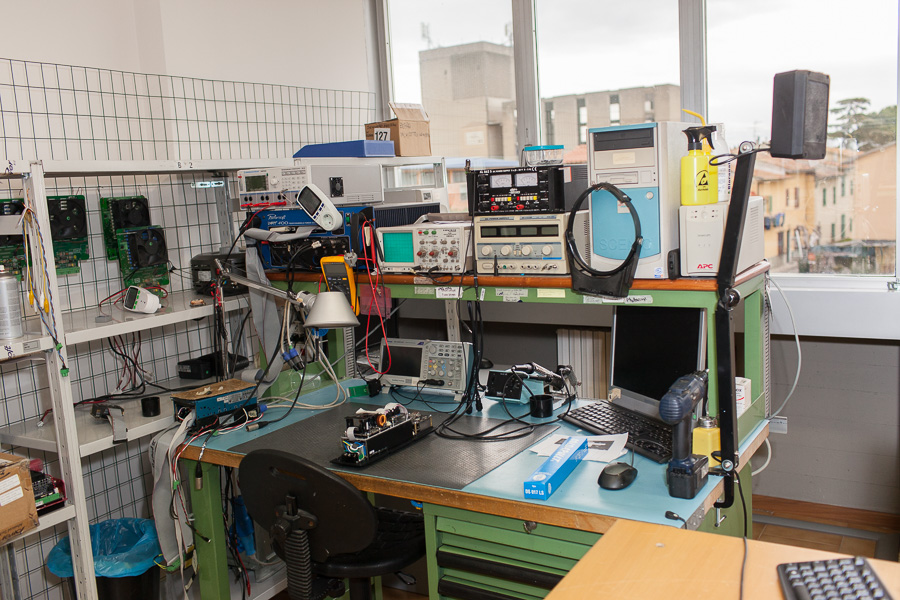
Les nouveaux produits comme les X (4 et 8) sont aussi rapatriés car ils embarquent une technologie très novatrice dont les éventuels défauts constatés par le SAV intéressent au plus haut point la R&D vers qui ils sont remontés.
Le soft des X étant ouvert vers l’extérieur, il sera à terme possible d’ausculter ces amplis à distance et pouvoir décider si la panne est réparable en envoyant des pièces ou s’il faut rapatrier l’appareil à Scandicci. Même s’il ne s’allume plus, il suffit de vider la mémoire des logs comprenant le suivi d’un très grand nombre de points de mesure et de paramètres, pour connaître à coup sûr quel a été l’événement qui a provoqué la panne.
Marco nous a cité un cas de figure où le log a permis de mettre au jour une utilisation assez peu orthodoxe d’un X8 en Amérique du Sud puisqu’on a retrouvé trace d’une puissance de sortie nominale de 40 kW sur une impédance de 0,9 ohm, soit vraisemblablement 8 subs sur un canal !! Chaque ampli qui quitte l’atelier repasse la batterie de tests finaux comme s’il venait d’être assemblé et le banc de mesure a été standardisé par Antonio pour l’ensemble de la société, du SAV à la fabrication en passant par la R&D afin que tout le monde parle le même langage.
M-FORCE et finesse
Dernière partie de notre périple au pays de la puissance sans fin mais en rack ultra-fin, nous avons été jeter un coup d’oreille dans l’auditorium de Scandicci où les techniciens de Powersoft dont Luca Gianni, le spécialiste applications audio de Powersoft et l’inévitable Mario di Cola, le consultant star de l’acoustique italienne, ont collaboré pour offrir au M-Force, un certain nombre de charges et d’ébénisteries d’évaluation différentes.
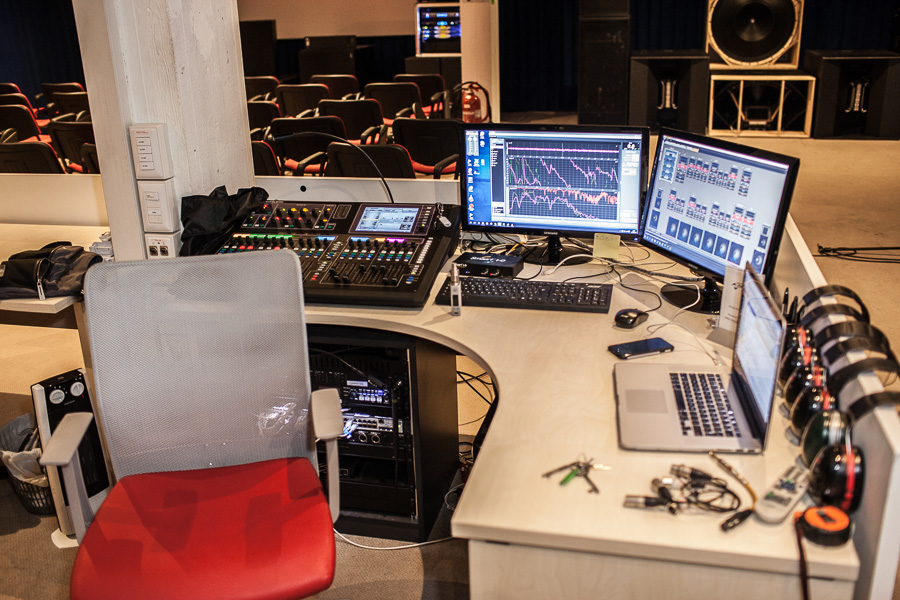
On a donc pu apprécier cet actuateur en trois versions différentes en compagnie de Luca Gianni qui a assuré la technique, et le comparer à des classiques subs double 18 » pour épauler des têtes de marque et modèle inconnus sur des titres que nous avons pris soin d’apporter. La surprise a été de taille. Contrairement à ce que l’on pourrait croire à la lecture des chiffres étourdissants et au côté « gros plastock » de la membrane du M-Force, le rendu est d’une justesse et d’une rigueur absolue, surtout comparé aux 18 » qui apparaissent en comparaison lents, trainant un boulet et manquant de définition et d’impact.
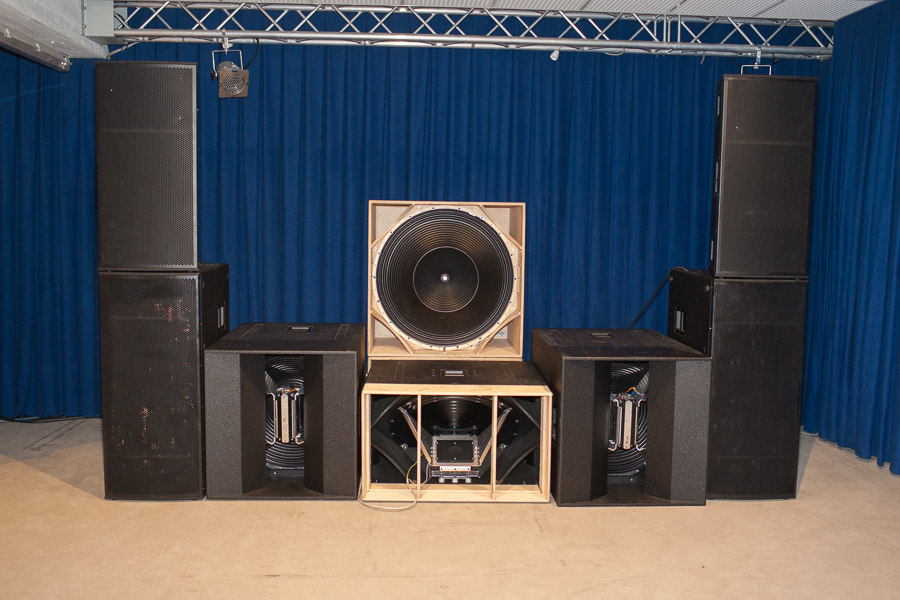
Oui la puissance est sans limite et nous ne nous sommes pas aventurés dans le déraisonnable, ce qui chez Powersoft peut être fatal, mais avec le M-Force on n’a pas le sentiment d’être devant une brute épaisse qui ne respecte pas le signal à reproduire, tout le contraire.
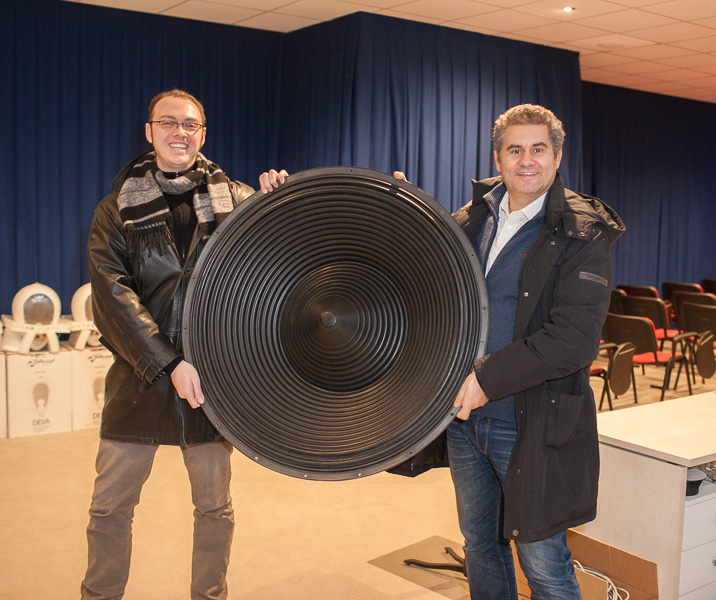
Des trois charges proposées, c’est la plus directe et la plus courte qui a le mieux mis en valeur les qualités acoustiques du M-Force et son rendu analytique des basses et très basses fréquences, même si ce n’est certainement pas celle qui lui permet de délivrer le SPL le plus élevé.
La possibilité d’intervenir sur les filtres et les pentes nous aurait permis de mieux encore appréhender ce système plus qu’original de reproduction du son, malheureusement nous avons dû repartir en direction de l’aéroport avant que le carrosse d’Antonio ne se retransforme en citrouille.
Chapeau quoi qu’il en soit à Powersoft, le M-Force n’est pas qu’un White Paper ou une machine à coups de boule juste bonne à tabasser des clubbers en mal de sensations, même si cela semble hélas être sa destinée.
Conclusion
En conclusion un très grand merci à toutes les équipes de Powersoft, et à notre guide Antonio Peruch, pour leur accueil et disponibilité de tous les instants lors de cette visite d’une rare transparence de laquelle on est sorti plus que convaincu quant au savoir-faire et à l’innovation qui règne dans la proche banlieue de Florence. Scandicci mériterait d’ailleurs le surnom de « watt city ».
Si vous avez manqué l’interview de Claudio Lastrucci, l’homme qui amplifie plus vite que son ombre et qui a autant d’idées que de volts sous le capot, la piqure de rappel est ici. Foncez, c’est parfois un peu technique mais vous ne regarderez plus un ampli de la même façon après !