Nous avons vu que les premières technologies de vidéoprojection à partir d’une source externe (relais optiques) fonctionnaient en réflexion.
Mais les vieilles habitudes étant tenaces, les premières tentatives (dont l’une perdure sous la forme de LCoS), visaient à effectuer une modulation analogique de la lumière en chaque point d’image, soit directement (Eidophor et dérivés), soit par le truchement de la polarisation (Titus, D-ILA/LCoS).
La nouvelle approche que nous allons vous présenter opère une rupture brutale avec ces démarches, en exploitant une modulation de la lumière en tout ou rien (autrement dit, « numérique », terme odieusement galvaudé). Et plus extraordinaire encore, elle revient aux sources en utilisant un procédé mécanique, comme les systèmes de balayage à laser (on n’est plus à ça près, on a vu que la vidéoprojection faisait feu de tout bois pour arriver à ses fins).
Si ce procédé fonctionne et se présente actuellement comme à la pointe de la projection vidéo (et bientôt d’éclairage) en termes de performances, cela est dû aux progrès prodigieux accomplis ces 10 ou 15 dernières années par la technologie électronique intégrée.
Au début était le MEMS
Les fabricants de semi-conducteurs ont appris progressivement à réaliser sur les substrats ou dans leur épaisseur des structures de plus en plus complexes et variées. Le silicium (Note 1) , en particulier (qui est aussi l’un des éléments les plus répandus sur la Terre), est la base de l’immense majorité des semi-conducteurs (diodes, transistors, circuits intégrés, microprocesseurs, mémoires…).
Note 1 : le silicium (Si) se dit « silicon » (comme « Silicon Valley ») chez les anglo-saxons… qu’il ne faut surtout pas traduire par silicone, terme qui désigne en français des polymères analogues aux polymères organiques à base de carbone, mais dont l’atome principal est du silicium et non du carbone.
L’industrie en maîtrise le façonnage à l’échelle microscopique par divers procédés : croissance de couches (épitaxie), photogravure (microlithographie), diffusion, dépôts métalliques, passivation (oxydation superficielle), etc. Grâce à ces techniques qui gagnent en finesse et en précision, la microélectronique est capable d’implanter sur des tranches de silicium des structures de plus en plus petites (des gravures d’une finesse de 20 nm, soit 0,000 02 mm, sont réalisées industriellement sur les dernières générations de processeurs informatiques), le tout en réalisant un nombre de plus en plus grands d’opérations successives (c’est-à-dire de couches) superposées avec précision.
Forts de cette maîtrise des procédés de micro-usinage des semi-conducteurs au service de l’électronique pure, les chercheurs et les industriels du secteur ont commencé à envisager au début des années 1970 d’utiliser ces procédés pour réaliser des systèmes pas seulement électriques, mais aussi mécaniques.
Il est donc possible d’implanter à la surface d’un substrat (principalement semi-conducteurs, mais cela peut être aussi des métaux, des céramiques ou des polymères), des pièces mobiles, vibrantes ou oscillantes, des leviers ou des petits moteurs, façonnés avec ces techniques. Ceux-ci sont actionnés par des champs électriques (les distances étant microscopiques, les champs électriques ont la même efficacité que les champs magnétiques d’un moteur « normal ») ou modifient les champs électriques présents à la surface du substrat. Des phénomènes thermiques (qui, à cette échelle, ne présentent qu’une très faible inertie) peuvent aussi être utilisés.
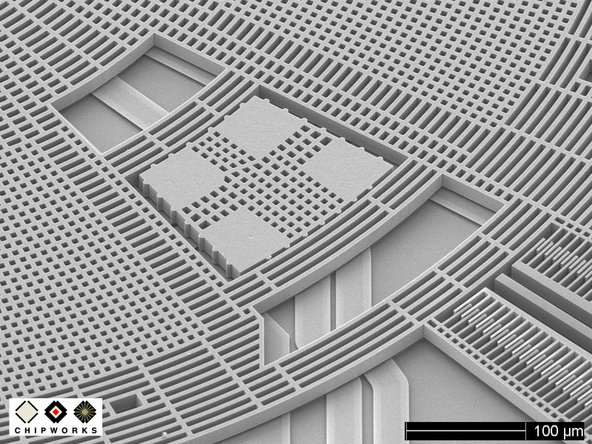
De tels dispositifs sont appelés MEMS (systèmes micromécaniques), et plus récemment, on voit apparaître des NEMS (c’est la même, chose, mais « nano » au lieu de « micro »).
Les premiers MEMS commercialisés au début des années 1980 étaient des capteurs de pression, et ces composants se sont extraordinairement diversifiés (accéléromètres, gyroscopes (voir figure 1), capteurs de champs magnétiques à effet Hall, microphones, oscillateurs à diapason, etc.) et ont gagné le domaine optique (MOEMS ou optical MEMS) et la biologie/médecine (bioMEMS).
Imaginée à la fin des années 1970 pour des imprimantes, les matrices de micro-miroirs ont été appliquées à la projection vidéo suite aux travaux de Larry Hornbeck de la société américaine Texas Instruments (Note 2) , qui a implanté une matrice de micro-miroirs sur un circuit intégré CMOS (1987), la rendant ainsi compatible avec l’électronique numérique standard.
Note 2 : Larry Hornbeck a reçu un Oscar pour ses travaux sur le DMD. Voir https://spectrum.ieee.org/tech-history/silicon-revolution/chip-hall-of-fame-texas-instruments-digital-micromirror-device.
Le composant à micro-miroirs
Le cœur d’une matrice de micro-miroirs est constitué d’un support semi-conducteur, qui est une mémoire statique (SRAM) CMOS implantée sur un substrat de silicium. Chaque cellule de cette mémoire dispose de deux sorties complémentaires reliées à des électrodes. Le dispositif mécanique est micro-usiné dans des dépôts d’aluminium successifs, déposés et gravés à l’intérieur d’une couche dite sacrificielle, qui est éliminée en fin de cycle de fabrication. Plusieurs couches successives (niveaux de métallisation) sont nécessaires pour obtenir le résultat final.
Dans les premières réalisations, chaque micro-miroir était constitué d’un carré en aluminium, maintenu au-dessus du substrat par deux minces lamelles de métal souples partant de deux coins opposés, jouant à la fois le rôle de support et de ressort de rappel fonctionnant en torsion. Le miroir fonctionnait lui-même comme moteur, étant attiré par l’une des deux électrodes affleurant du substrat sous les angles libres du miroir (voir figure 2). Puis les niveaux de métallisation se sont multipliés pour donner lieu à des structures plus complexes et plus performantes.
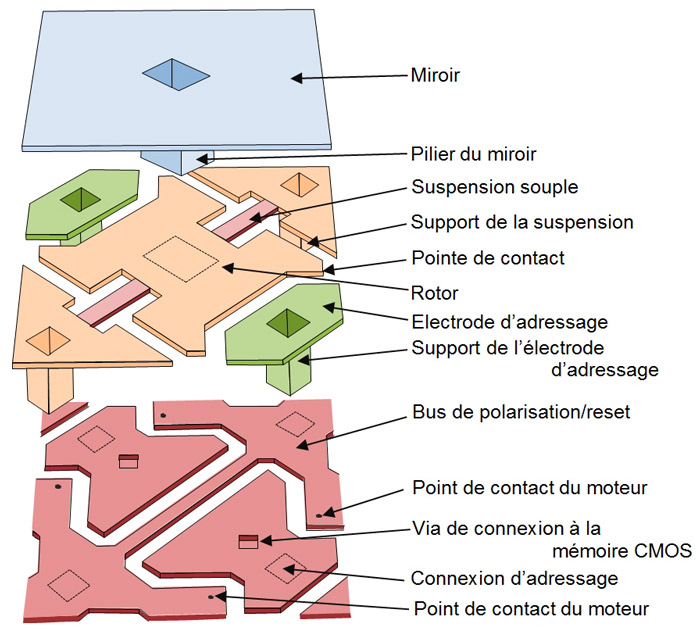
Dans l’approche actuelle, le « moteur » est sur un niveau séparé. Il est constitué d’une surface d’aluminium solidaire de deux lamelles métalliques élastiques, jouant le rôle de suspension et de ressort, fixées au-dessus du substrat via deux piliers en aluminium. Les électrodes sont elles aussi surélevées. Elles permettent à la plaque motrice de basculer autour de l’axe de rotation déterminé par les lamelles ressort.
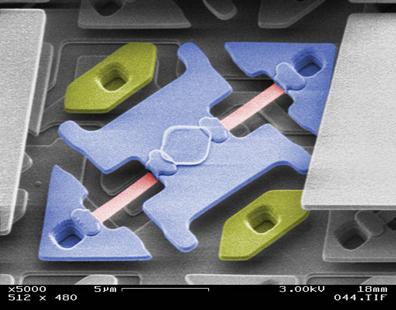
Celle-ci possède, de part et d’autre de chaque électrode, deux prolongements souples (landing tips) qui viennent en contact avec le substrat quand le moteur bascule complètement du côté de l’électrode active (voir figure 3).
Le miroir lui-même est une surface carrée d’aluminium réfléchissant, fixée au moteur précédemment décrit par un pilier placé en son centre. La surface du miroir est plane est uniforme, à l’exception d’une dépression centrale à l’endroit du pilier de fixation.
L’intérêt de multiplier les niveaux de métallisations est de permettre d’avoir des miroirs quasiment jointifs (malgré leur basculement) et de permettre l’augmentation de l’angle de rotation. De 10° dans les toutes premières versions, on est passé à 12°, puis maintenant à 17°. L’avantage est de donner un meilleur contraste grâce à une séparation plus nette des faisceaux correspondant au noir et au blanc. La taille des miroirs est de quelques micromètres (millièmes de millimètre).
Fonctionnement optique du relais optique à micro-miroirs
Chaque miroir de la matrice DMD est bistable et peut prendre, lorsque le circuit est sous tension, deux positions symétriques de part et d’autre de l’axe du substrat. L’angle est de ±10, ±12 ou ±17° selon la génération du composant. La source collimatée et l’objectif de projection sont disposés de telle matière que dans l’une des orientations du miroir, dite « ON », la lumière de la source soit envoyée vers l’objectif, et dans l’autre position, dite « OFF », la lumière de la source est envoyée hors de l’objectif (voir figure 4) et se perd sur un « dissipateur ».
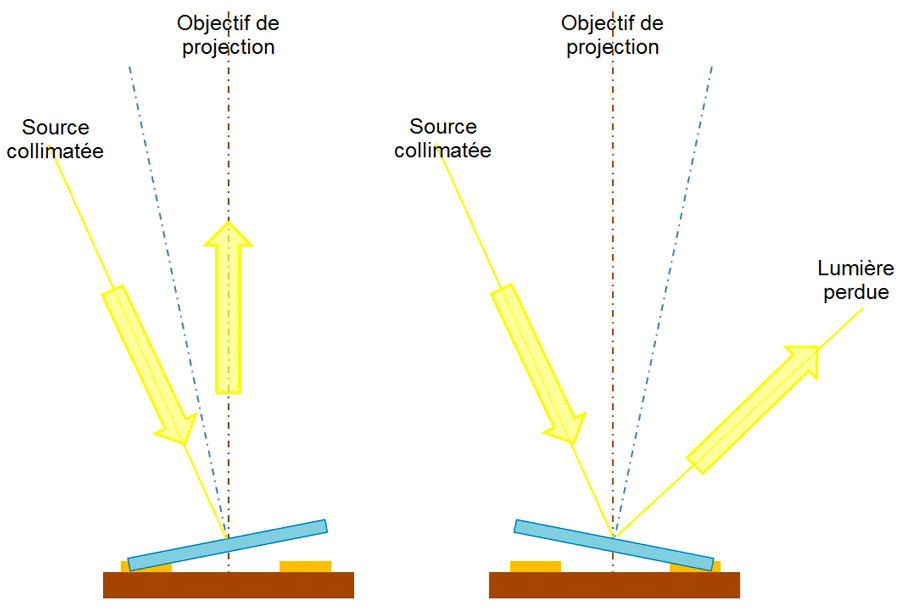
Il s’agit d’une surface noire mate qui absorbe toute la lumière et la transforme en chaleur, évacuée avec les fluides de refroidissement. Le fonctionnement est donc en tout ou rien (d’où le premier « D » de « DMD »). Vu de l’écran, chaque point de l’image, représenté par un miroir, est totalement allumé ou totalement éteint, le micro-miroir ne génère pas directement les « niveaux de gris ».
Pour obtenir toute une gradation avec les niveaux intermédiaires, on procède par modulation de durée, c’est-à-dire que le miroir, capable de basculements très rapides, oscille entre ses deux positions, de manière à ce que l’œil, qui a un comportement intégrateur et passe-bas, ne perçoive que la moyenne.
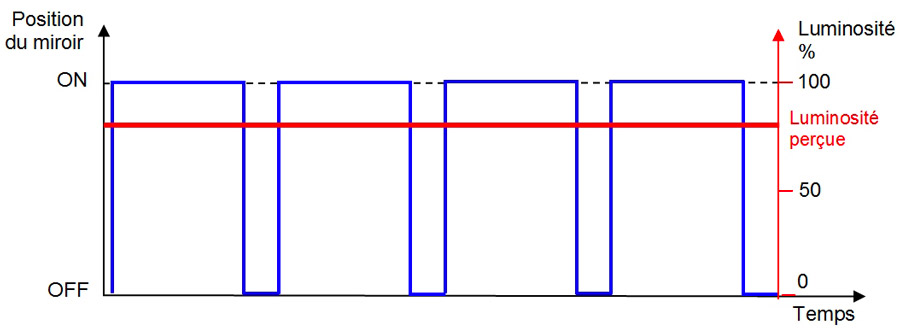
Ainsi, si, dans une séquence répétitive de période TON + TOFF, TON est le temps pendant lequel le miroir est dans la position ON, et TOFF dans la position OFF, l’œil perçoit un niveau intermédiaire équivalent à TON/TOFF (voir figure 5).
Ce principe est similaire à celui de la modulation de largeur d’impulsions (PWM), utilisée dans la plupart des amplificateurs de puissance audio et des convertisseurs d’énergie en classe D. Dans le domaine de la visualisation, la technique est assez bien éprouvée, puisqu’elle s’apparente à celle qui est mise en œuvre dans les écrans à plasma, dont chaque cellule n’a que deux états possibles (allumé ou éteint), sans niveau intermédiaire (avec, dans ce cas, une difficulté supplémentaire due à la nécessité de générer des signaux à haute tension).
Si on souhaite afficher des niveaux de luminosité sur 10 bits, il faut être capable de maîtriser la durée des impulsions de commande de chaque miroir avec une résolution de 1/1024 (soit près de 0,1 %), ce qui n’est pas évident compte tenu du nombre de miroirs à piloter individuellement (21,2 millions en 2K) et de l’ordre de grandeur des durées (inférieures à la milliseconde).
Moteur optique DMD monochrome
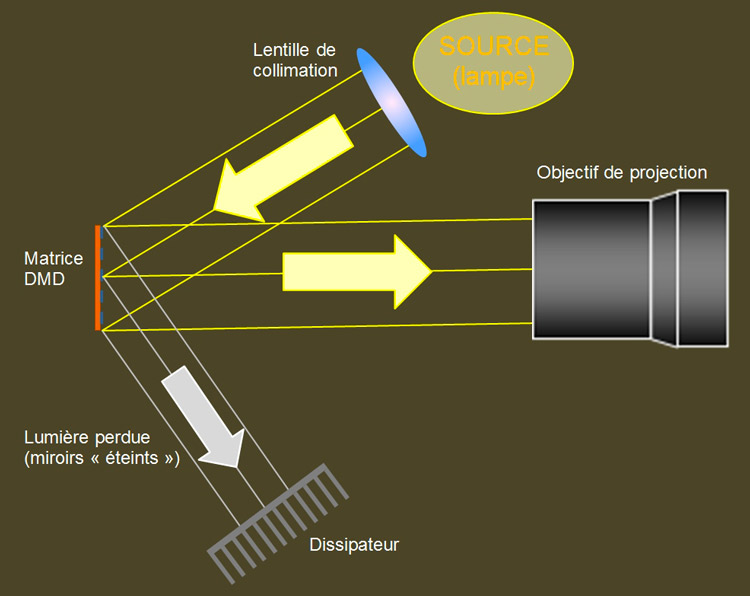
On peut réaliser simplement un moteur optique DMD monochrome en exploitant directement les propriétés explosées ci-dessus, les faisceaux lumineux incidents et réfléchis se propageant naturellement dans l’air (voir figure 6).
L’avantage de ce système est sa simplicité et sa légèreté. L’un des inconvénients de ce procédé est que la source lumineuse et l’objectif de projection risquent d’être proches, aboutissant à une configuration mécanique « bizarre ». On est donc amené à introduire des miroirs de renvoi qui compliquent le système.
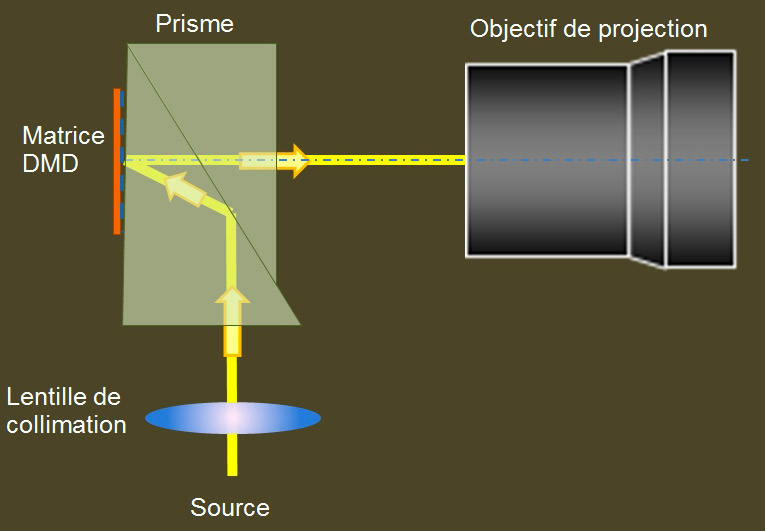
Une approche différente consiste à utiliser un prisme taillé de manière particulière de manière à introduire la lumière de la source latéralement (voir figure 7).
Cette disposition ressemble un peu au PBS des LCoS, mais les angles ne sont pas les mêmes. Le système obtenu est plus compact, plus facile à implanter dans un projecteur et donne lieu à des réalisations scellées. L’image DMD présente une structure moins flagrante que l’image LCD, mais un peu plus caractérisée que l’image LCoS.
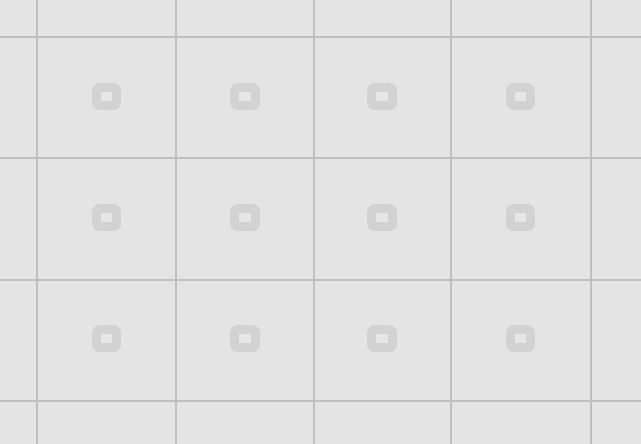
L’espace noir entre les miroirs est très fin et difficile à discerner. Les « pixels » se manifestent plus par le point un peu plus sombre correspondant à l’image de la dépression centrale au niveau de fixation de chaque miroir (voir figure 8).
Il faut bien reconnaître que, sur les réalisations modernes en haute résolution, même sur grand écran et avec le nez dessus, ces détails sont peu visibles et tombent probablement sous la limite de diffraction des optiques de projection.
Moteur optique couleurs à un seul DMD
Bien sûr, les systèmes monochromes ne sont plus qu’un cas d’école et la couleur est incontournable depuis des lustres. Toutefois, il est facile (et ce d’autant plus avec les technologies numériques modernes) de transformer un système monochrome suffisamment rapide en système trichrome, voire quadrichrome (et plus si affinités) par l’ajout d’un disque de filtres colorés, à l’instar de ce qui se faisait dès les tout premiers Eidophor.
A l’aide de mémoires d’image, le traitement d’image affiche successivement les images correspondant aux trois primaires rouge, vert, bleu (et éventuellement à un 4eme canal), tandis que la matrice est illuminée de manière synchrone successivement avec une lumière correspondant à la composante affichée. Il s’agit donc d’un procédé de couleurs séquentiel.
Le cycle doit se répéter au minimum à la fréquence image c’est-à-dire que pour 60 Hz (période 16,666… ms), la fréquence de fonctionnement de la matrice doit être au minimum de 180 Hz (3 canaux) ou 240 Hz (4 canaux), soit des périodes d’affichage respectives de 5,555… ms ou 4,166… ms. Mais comme on a pris l’habitude de rafraîchir l’image à fréquence double (120 Hz), triple (180 Hz), ou même quadruple (240 Hz), voire plus encore lorsqu’il s’agit de produire des images en 3D relief, on arrive rapidement à des cadences d’affichage infernales.
L’effet arc-en-ciel est un artefact qui se manifeste sur les systèmes à couleur séquentielle, donc sur les projecteurs mono-DMD. Effet psychovisuel, il ne peut être ni quantifié objectivement, ni photographié, et son importance dépend des individus. Certains y sont très sensibles, d’autres ne le perçoivent pratiquement pas. Il consiste en l’apparition fugitive de surfaces diversement colorées accompagnant les objets en mouvement rapide. On pense que l’œil anticipe les mouvements dans l’image et dans ce suivi rapide, il perçoit les images intermédiaires dans les différentes couleurs, qui seraient mal intégrées et moins bien fusionnées à l’objet suivi.
Certaines personnes éprouvent également des difficultés (se manifestant par de la fatigue visuelle et des maux de tête) avec la commutation en tout-ou-rien des points image. Ces deux effets s’atténuent considérablement avec les systèmes récents à doublage ou quadruplement d’images. La solution en effet, consistant à réaliser plus rapidement ce « leurrage » psychovisuel aboutit à une intégration plus parfaite de la luminosité et des couleurs, à tel point qu’on peut même travailler avec des images en 3D relief sans éprouver de gêne (autre que celle due aux lunettes).

La réalisation de ces systèmes peut emprunter plusieurs voies. Avec une source à lampe, il est d’usage d’utiliser un disque de filtres rotatif (désormais connu sous l’appellation « color wheel », servilement traduite par « roue de couleurs ») synchronisé sur le traitement du signal (voir figure 9).
Placé sur le trajet de la lumière entre la source et la matrice, à un emplacement où le faisceau est relativement concentré, ce disque peut être de taille réduite, donc à faible inertie, et se contenter d’un tout petit moteur. En revanche, il peut être sujet à des problèmes thermiques. Dans le cas où l’affichage s’effectue avec un doublage ou quadruplement d’images (120 ou 240 Hz), on peut doubler le nombre de secteurs du disque de couleurs pour en réduire la vitesse de rotation.
Avec les sources « solides », il y a plusieurs approches possibles. Soit on utilise un deuxième disque de couleurs synchronisé, portant des secteurs de phosphores et des secteurs neutres dans le cas laser-phosphore (voir l’épisode Les sources solides à led et lasers 2ème partie), soit dans le cas des LED ou de certaines configurations laser, on utilise directement les capacités de commutation rapide de ces sources solides, qui sont alors pulsées par des commandes issues du traitement. Il s’agit d’une solution d’avenir qui s’affranchit de tout dispositif mécanique (comme dans la configuration hybride laser-phosphore/LED de Panasonic)
Conséquences sur le flux
Dans un système trichrome (R,V,B), pour chacune des primaires, l’image n’est affichée (dans le meilleur des cas) que durant 1/3 du temps. L’effet intégrateur de l’œil joue encore ici, et sa conséquence est que, pour chaque primaire, la sensation lumineuse n’est que le tiers de ce qu’elle serait si chaque couleur était affichée en permanence.
Par conséquent, par rapport au potentiel de la source de lumière, la sensation est divisée par trois. Ou, autrement exprimé, pour obtenir le même flux qu’avec une technologie à 3 matrices similaires fonctionnant simultanément (comme avec le 3LCD par exemple), il faut multiplier par trois le flux de la source (c’est-à-dire sa puissance électrique et la chaleur produite). Par conséquent, la technologie mono-DMD est certes économique, mais elle est plus limitée que les autres technologies en termes de puissance lumineuse.
Ajout d’un canal supplémentaire
Pour contourner le médiocre rendement lumineux et la limitation du flux, les constructeurs usent d’une astuce qui se fonde sur l’observation des images réelles. En effet, lorsque les images sont issues d’une captation (et non d’une création graphique ex nihilo), on ne trouve pratiquement jamais de parties d’images qui présentent à la fois une forte luminosité et une forte saturation.
En revanche, les parties claires, voire très claires, sont souvent peu saturées (grossièrement, ce sont des blancs et non des couleurs vives). Forts de cette observation (qui peut parfois être prise en défaut), les fabricants ont décidé d’ajouter un quatrième canal de « couleur » dans la séquence de projection. Ce canal a pour fonction de renforcer la luminosité des images très claires.
Par conséquent, il donne, sur les mesures de flux traditionnelles (ANSI et similaires), des chiffres plus honorables, mais en cas de couleurs vivres à forte intensité (images de synthèse notamment, mais pas seulement), les projecteurs ainsi conçus montrent des faiblesses (images délavées ou détails écrasés dans les zones très colorées).
Pour cette raison a été instituée la mesure de luminosité des couleurs (Color Light Output, CLO ou Color Brightness, voir chapitre Spécifier un projecteur : Spécifications relatives à l’image), obtenue en calculant la somme des luminosités obtenues sur des plages de couleurs R, V, B saturées à 100 %. Un écart sensible entre la mesure conventionnelle de luminosité (effectuée sur du blanc à 100 %) et la mesure CLO trahit la présence d’un 4eme canal.
La réalisation de ce canal supplémentaire dépend de la technologie de la source. Avec une source à lampe, il suffit de ménager sur le disque de couleurs un secteur totalement transparent. Le 4eme canal est donc blanc. Il appartient aux fabricants de le doser avec tout le doigté nécessaire en choisissant la largeur du secteur blanc qui réalise le meilleur compromis entre le flux ANSI désiré et des caractéristiques honorables sur les images fortement colorées.
Avec les sources solides, le 4eme canal est habituellement jaune (vert + rouge), étant donné que la contribution du bleu à la luminosité du blanc est marginale. Il est réalisé par une combinaison entre un secteur du disque de phosphore et un secteur transparent du disque de filtres de couleur dans la technologie laser-phosphore.
Les flux les plus élevés réalisables actuellement sur des projecteurs à une seule matrice DMD se situent entre 15 000 et 20 000 lumens, mais le plus gros de l’offre se situe toujours largement au-dessous de 10 000 lumens (ANSI). Les flux CLO ne sont jamais indiqués. Notons que contrairement aux autres technologies, le DMD(DLP) reste une technologie propriétaire et exclusive de Texas Instruments.
Pour en savoir plus, une collection de très belles images de matrices DMD en microscopie électronique à balayage (SEM) réalisées à l’institut d’Optique de l’Université de Rochester assorties, de quelques explications est visible avec ce lien
Glossaire contextuel
La suite… Dans le prochain épisode, nous approfondirons le fonctionnement des composants DMD (DLP) et nous détaillerons les configurations à trois matrices DMD, qui permettent les plus hautes performances disponibles actuellement en vidéoprojection. Nous terminerons cette partie par un comparatif des technologies et un tour d’horizon du marché des vidéoprojecteurs professionnels destinés aux usages qui nous intéressent.
Et avec les épisodes précédents :
- Lien Ep1 : La vidéoprojection face aux écrans, les compromis sur l’image
- Lien Ep2 : La vidéoprojection face aux écrans led, à chaque environnement sa solution
- Lien Ep3 : Spécifier un projecteur : Spécifications relatives à l’image
- Lien EP4 : Spécifier un vidéo projecteur : Placement, installation, environnement et ergonomie
- Lien EP5 : Spécifier un vidéo projecteur : Des interfaces vidéo pour la vidéoprojection
- Lien EP6 : Spécifier un projecteur : des interfaces vidéo à très haute résolution
- Lien EP7 : Les sources de la vidéoprojection-Première partie : Les lampes
- Lien EP8 : La vidéoprojection dans tous ses états : Les sources solides LED et Lasers
- Lien EP9 : La vidéoprojection dans tous ses états : Les sources solides LED et Lasers 2ème Partie
- Lien EP10 : La vidéoprojection dans tous ses états : Part Three: Mettez de l’optique dans votre moteur! LCD part 1
- Lien EP11 : La vidéoprojection dans tous ses états : Part Three: Mettez de l’optique dans votre moteur! LCD part 2
- Lien EP12 : La vidéoprojection dans tous ses états : Part Three: Mettez de l’optique dans votre moteur! D-ILA, LCOS, SXRD ET Compagnie